Natara’s Journey to Operational Excellence
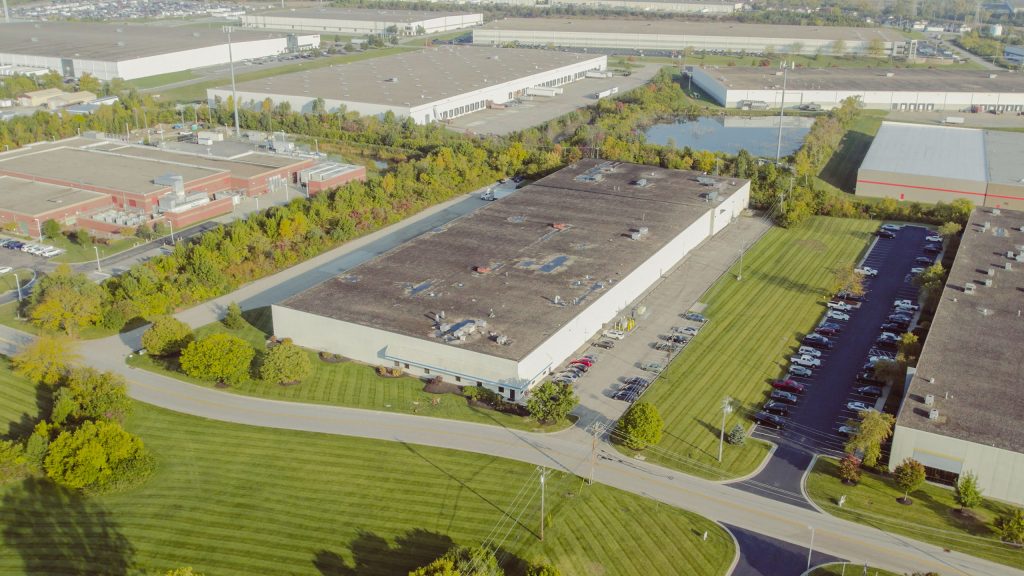
At Natara, we believe that operational excellence isn’t just a goal — it’s the foundation of how we deliver value to our customers worldwide. After establishing key fundamentals in 2024, we’re accelerating key developments throughout 2025 to enhance our global operations and elevate service excellence. Nick Pennell, our Vice President of Transformation, explains how the 2024 advancements are creating a stronger, more agile Natara — and how they pave the way for an even brighter future.
2024: Delivering Results Through Strategic Enhancements
This past year, Natara made significant investments to optimize its supply chain, focusing on production capacity, operational leadership and streamlined processes.
Cincinnati: Doubling Capacity for Reliable Supply and Faster Delivery
At our Cincinnati manufacturing facility, we have invested both in our people and equipment to meet growing demand. “One of the major changes we’ve implemented is adding a second operational shift and debottlenecking capacity,” explains Nick. “Previously, the site operated on a single shift, but by adding a second shift, we’ve increased efficiency and significantly reduced lead times.” Further improvements included automating manual processes like material charging and discharging.
Through these enhancements, production output has increased significantly, boosting our On-Time In-Full (OTIF) performance and customer satisfaction.
Teesside: Leadership Driving Operational Excellence
At our Teesside site, new leadership and a focus on advanced planning have significantly enhanced operational capabilities. “The addition of Andrew Horkan as Site Operations Director and Karl Nugent as Supply Chain Manager has brought fresh perspectives and a sharper focus on operational excellence,” explains Nick. “Their leadership has been pivotal in improving planning processes, resulting in better delivery timelines and more reliable service for our customers.”
Streamlined Sales and Operations Planning (S&OP)
Across all manufacturing facilities, a structured S&OP framework, led by our new Global Supply Chain Director Mark Joyce, has addressed multiple challenges in balancing demand with production capabilities. “Our transition to a more structured S&OP framework allows us to better align our production planning with market demand,” Nick explains. “Classifying products into Make to Stock (MTS) and Make to Order (MTO) categories allows us to deliver high-demand products faster while maintaining readiness for less frequent orders.”
With this new approach, Natara is achieving greater alignment between sales forecasts and production capabilities, increasing reliability of supply.
2025: Building on Momentum for Future Success
Looking ahead, Natara is set to build on its 2024 achievements with initiatives designed to enhance capacity, efficiency and customer satisfaction further.
Infrastructure Upgrades to Boost Reliability and Sustainability
Both Teesside and Hartlepool will benefit from infrastructure investments. “Upgrading Teesside’s boiler systems will improve uptime and energy efficiency,” explains Nick. “Meanwhile, our Hartlepool facility will undergo critical infrastructure enhancements to support increased production demands. Last year we installed two new vessels in Hartlepool, in 2025 we’re making plans to further accelerate infrastructure upgrades to ensure reliability and scalability.”
Expanding MTS and MTO Segmentation Across All Sites
In 2025, Natara will be expanding its MTS vs. MTO segmentation globally to deliver clearer, faster, and more predictable lead times. “Christopher Surrao, Director of Operations & Supply Chain at the Cincinnati facility, has successfully implemented the MTS and MTO models at the Cincinnati site,” explains Nick. Building on Cincinnati’s success, Natara is setting the stage for a global rollout, driving supply chain efficiency and delivering a faster, more reliable customer experience.
Oracle ERP Upgrade to Enhance Planning Capabilities
An upgraded Oracle ERP system will streamline planning, eliminate manual steps and improve response times — delivering a faster, more seamless customer experience. “With this system, our teams will have instant access to production schedules and inventory, enabling real-time updates for customer inquiries,” notes Nick.
Commitment to Excellence
“While Natara has made great progress, we’re not stopping here,” concludes Nick. “We’re committed to a journey of transformation through which we are confident in our ability to not just meet, but exceed customer expectations in the years ahead.”
Stay tuned as Natara continues its journey to set new standards for operational excellence!